Wait, what now, glowing googley
eyes?
|
|
|
Fairly
simple right? glowy googley eyes. So here's last year's starting point.
The eyes were an afterthought to add a bit more character to the
contraption. In these photos i was mostly moxking up where they looked
reasonable and how far off the impeller they should live. These are
taped in place in this image. The actual support is some opaque white
acrlyic sheet, heat-bent into shape. |
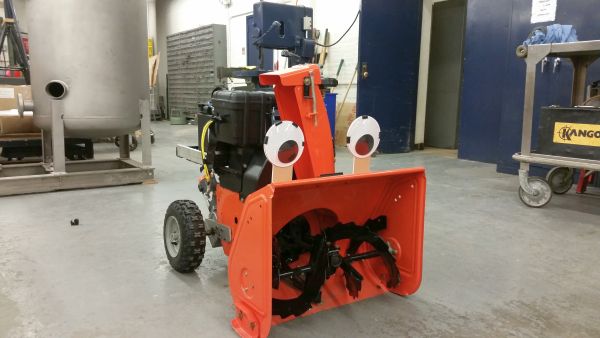 |
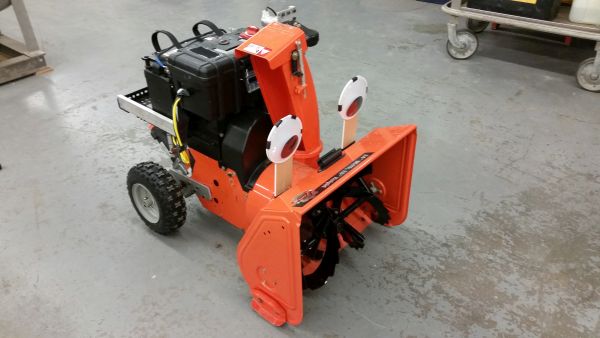 |
I did some digging. Initially I
had plotted using those 'amazon esque' extruded
aluminum light blobs, but no matter where I placed them, it made the
setup look a bit cluttered. Some ebay hunting later, and behold weirdo
hi-hat lights. These were
found on ebay [link]. But without useful
dimenions there were a few things to be sorted. |
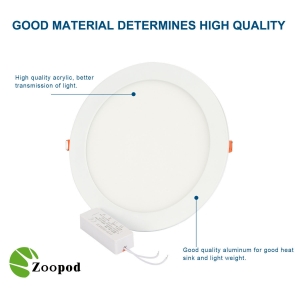 |
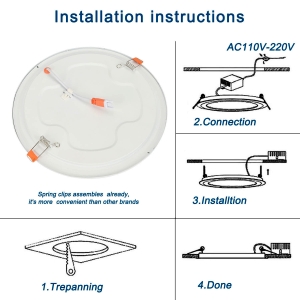 |
After about a week, the lights
appeared. They are impressivley
thin. While
these are listed as 110-220vac, I guessed that they would have an
external inverter to drop things down to a reasonable led drive
voltage. They appeared and at first I was impressed, 20$ for 4 lights,
at 18w each? Tell me more. It looks reasonable and i initially imagined
a single PCB with a pile of small white leds and a lot of
diffuser. |
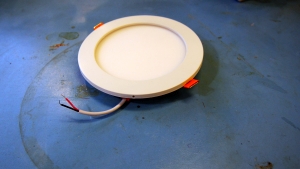 |
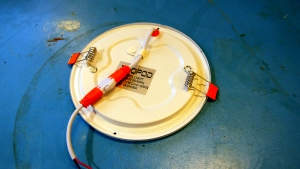 |
The
light fixtures are incredibly thin, honestly I was impressed. The
inverter to power the light was also, maybe 50 grams and 4 times as
thick as the fixture. Time to take these apart and see what makes them
tick. |
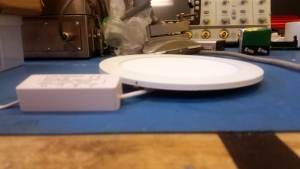 |
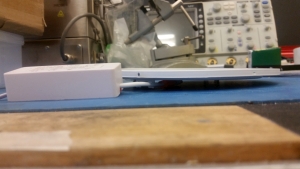 |
I
had orderd both the 18w 6" version and the 12w 4" version
of these things. The 18w lights themselves were too big to use
un-modified. The outer ring was decorative for celing installtions,
just made the eyes look goofy. I began the process of opening the 18w
light up to investigate how I could go about modifying it for
my
application. This is where i was earnestly
surprised, Its
just two stamped parts and an led strip. Mechanically that is it. No
PCB, just a giant circular difusser. |
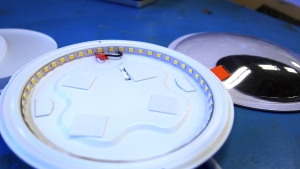 |
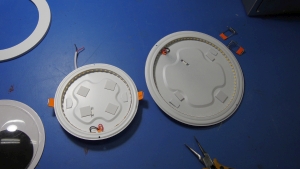 |
While
the design is lackluster it does fit the bill. It is bright, and
impresivley evenly distributed lighting. No pointy white bits visible,
just an orb of light. |
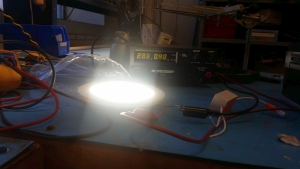 |
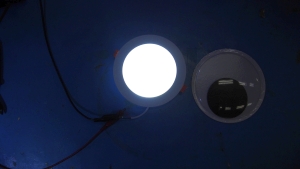 |
As
i had mentioned, the fixture alone was a bit oversized for a 6"
diameter googley eye, however the actual LED strip was remarkably close
in size in relation to the blow moulded googley eye cover (shown far
right). |
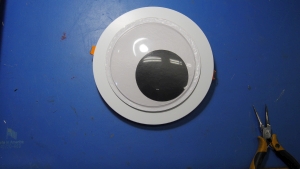 |
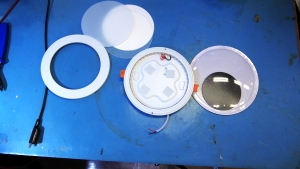 |
Wait,
how do they get the light so uniform? I didnt really pay attention here
until i thought about it. There's actually 3 layers. The base is a
reflective white disc. This allows the base of the actual fixture to be
off-white and odd shapen. The base disc is floppy but serves as a white
reflective surface. The second layer mates the light output from the
leds and the outbound optic. Finally the thrid layer is a diffuser,
removing any of the discrete led ring features and making the orb
uniform in brightness. Without these its just a ring of leds (shown far
right). |
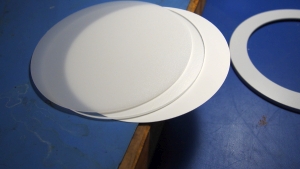 |
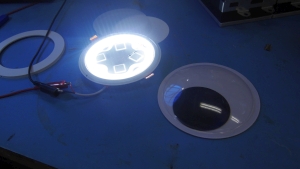 |
Some
quick solidworks modeling later, I had a plan for a new enclosure for a
trimmed down 18w fixture |
|
|
With
the model in and and DXF-ifyied, i headed to the lasercutter and cut
out two sets of white acrylic 3mm googley eye-light fixture holders |
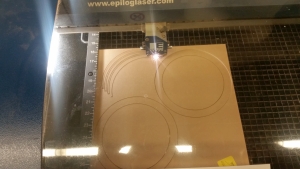 |
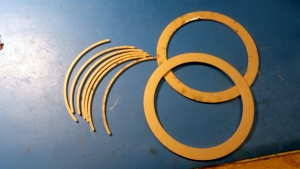 |